validation Testing
Ensuring the highest quality every time
Because there is no governing body that specifies seal validation requirements, you need a seal supplier you can trust to use only the best materials and produce the most reliable seals for your application. Amsted Seals has a wide range of testing capabilities that allow us to do just that – continually produce the highest quality seals with proven performance.
Rubber validation testing
Compound immersion testing – a series of elastomeric compound tests for compatibility with application fluids to understand the impact of time and temperature on mechanical properties – are typically conducted using ASTM 471-12a and 395-B methodology.
Rubber validation equipment:
- Tensile tester
- Moving Die Rheometer
- Thermogravimetric Analysis (TGA)
- Fourier Transform Infrared Spectroscopy (FTIR)
- Differential Scanning Calorimetry (DSC)
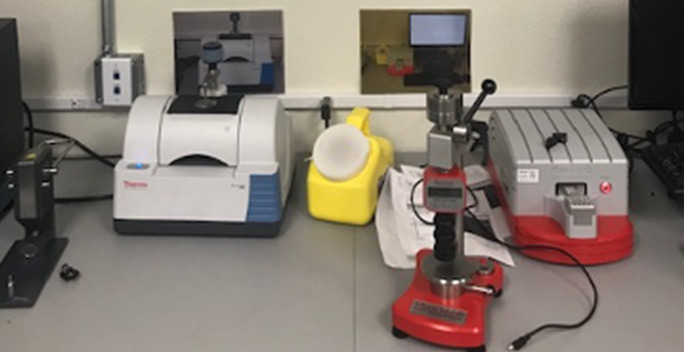
Seal validation testing
Functional rig tests on actual seals and seals alone. These tend to be customer-specific relative to the duration and criteria for failure as well as number of samples per test.
Typical tests include:
- Hot life – Benchmark is the number of hours until 3.0 grams of fluid that has accumulated into a catch basin on the air side.
- Slurry – Benchmark is the number of hours for either ingress of slurry into the sump or egress of fluid into the slurry.
- Cold (-40°) – This is typically 10 thermal cycles after a specified cold soak. Leakage down the seal face is the typical mode of failure, but other tests include cracking and followability.
- Water spray – Similar failure criteria as for slurry.
- Customer in-house testing – Usually in assembled hubs with all components on axle spindles. These also tend to be customer specific relative to the duration and criteria for failure as well as number of samples per test.
- Fleet testing – Generally dictated by the truck manufactures and could include up to one year for full seasonal evaluation. These are tracked and closely monitored for any seal issues.
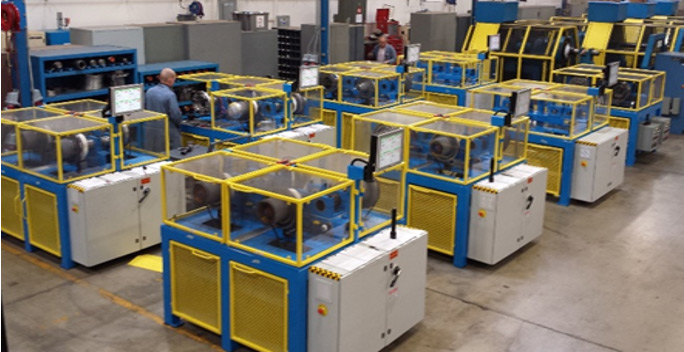